
Micro-CT scan confirmed that under 100% infill ratio, there are still some internal voids presented, regardless of the applied building orientation. Īpart from above noted printing parameters, the mechanical performances of PEEK products are significantly affected by the infill ratio, building orientation, and raster angle. investigated the relationship between various thermal processing conditions (the ambient temperature, the nozzle temperature, and heat treatment methods) in the FDM process and crystallinity and mechanical properties (tensile strength, elastic modulus, and breaking elongation) of pure PEEK material. The parameters of a heating temperature of 440 ☌, printing speed of 20 mm/s, and printing layer thickness of 0.1 mm are recommended to reduce the internal defects and improve the bonding strength and surface finish.

Moreover, the research from Hu and his colleagues show that the uniformity of temperature field during FDM printing was essential to ensure the high mechanical performance of PEEK, and a heat controller could be used to monitor the extrusion temperature.The melting condition and fluidity of PEEK during FDM fabrication were investigated by employing finite element analysis. showed that the chamber temperature has more influence on the warping deformation of FDM-PEEK samples than that the nozzle temperature does, and the warping deformation of FDM-PEEK samples reduces with increasing chamber temperature, whereas it has the tendency of a parabola going upwards with increasing nozzle temperature. investigated the effect of process parameters (chamber temperature, bed temperature, screw speed, deposition speed, standoff distance between nozzles, and bed surface) on layer bonding, layer thickness, and width during the fused layer modeling process. Because the temperature fluctuations directly affected interlayer bonding, Kumar et al. expressed that thermal conditions (e.g., extrusion temperature and ambient temperature) need to be carefully controlled in order to ensure good interlayer bonding and to minimize warpage and delamination. The results showed that the strength of the FDM-PEEK samples was approximately half of the tensile strength of molded PEEK. developed a new FDM machine to produce PEEK medical implants, and the mechanical properties of manufactured products were investigated. In order to investigate processing PEEK on a 3D printer for thermoplastic modelling, Valentan et al. Currently, the influence of printing parameters on the formability and mechanical properties are attracting more and more interest, which should be investigated thoroughly to enlarge the biomedical applications of FDM printed PEEK. However, a number of challenges still exist in successfully realizing FDM printed PEEK owing to its high melting temperature, great melting expansion, and especially its microstructural packing state. reported that fused deposition modeling (FDM) is the most commonly used and low-cost 3D printing technology for thermoplastic materials, which has been an alternative method to process PEEK parts. Among all the AM manufacturing methods, Gao W et al. Compared with traditional injection molding and extrusion technology, additive manufacturing (AM) offers a number of advantages for designing and manufacturing customized and complex functional parts with greater flexibility and low manufacturing cost. Polyether-ether-ketone (PEEK) is a potential biomaterial that could replace traditional metal or ceramic parts for biomedical applications due to its excellent biocompatibility and desirable mechanical properties. The findings of this study provide guidelines for FDM-PEEK to enable its realization in applications such as orthopedic implants. The results show that horizontal infill orientation with 30° raster angle is promising for a better comprehensive mechanical performance, and the corresponding tensile, flexural, and shear strengths are (76.5 ± 1.4) MPa, (149.7 ± 3.0) MPa, and (55.5 ± 1.8) MPa, respectively. Its main failure mechanism was correlated to the internal voids. In practice, FDM fabricated PEEK acted more like a laminate rather than a unified structure.
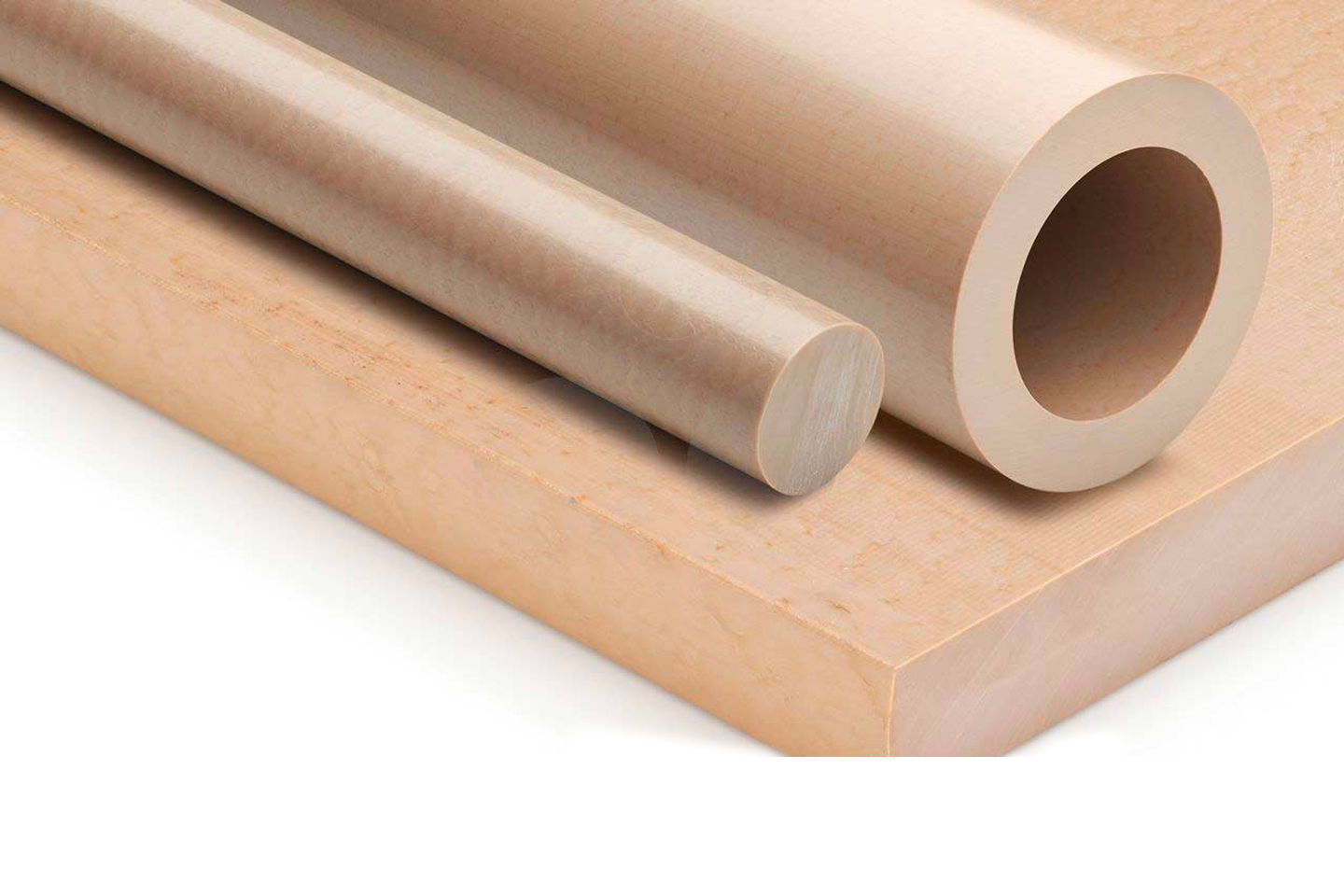
Raster angle has a significant effect on the mechanical strength but not on the failure mechanism. During the FDM process, the crystal unit cell and thermal attribute of PEEK material remained unchanged, whereas the surface layer generally became more hydrophilic with an obvious reduction in surface hardness.
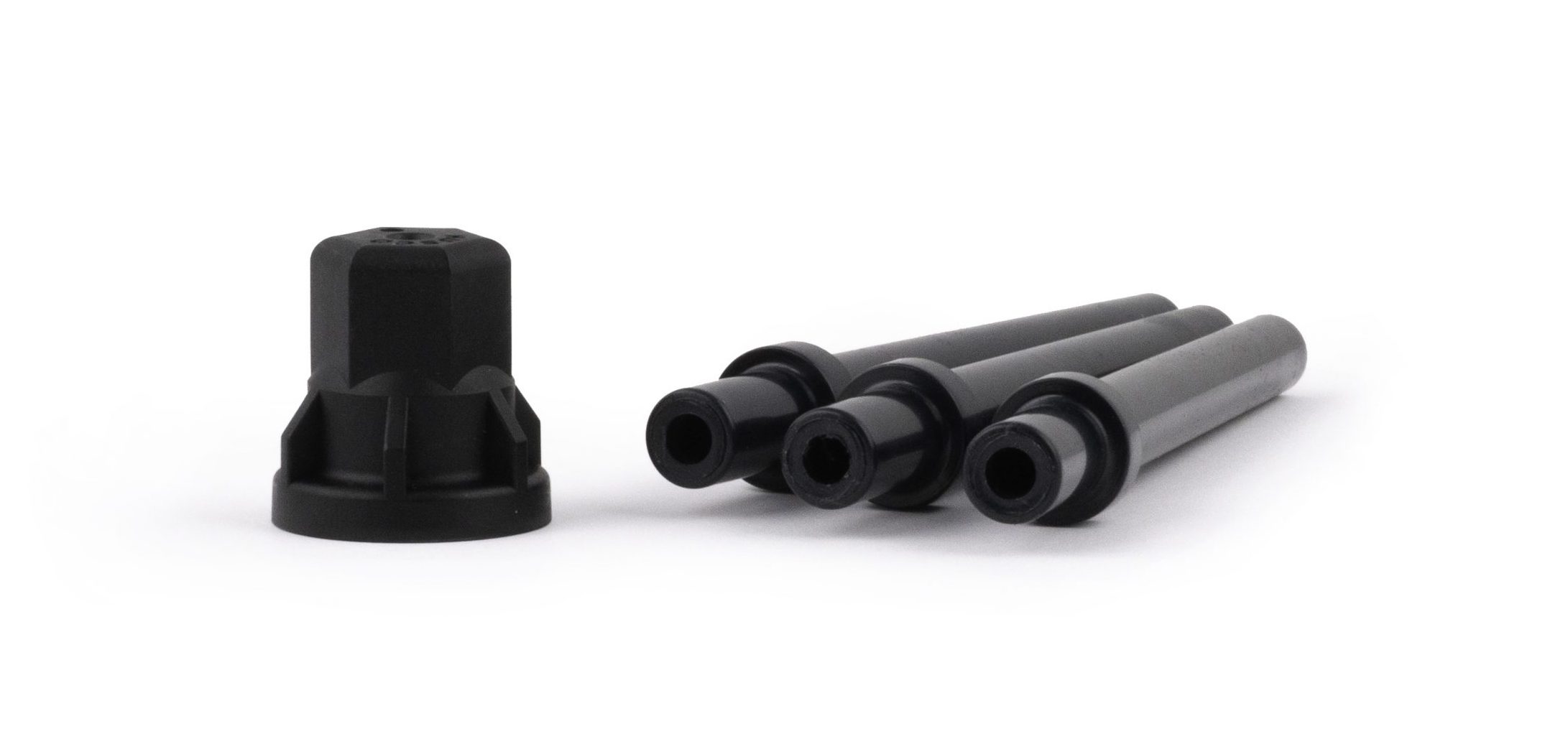
In this study, the surface characteristics, microstructure, and mechanical properties of fused deposition modeling (FDM) prepared polyether-ether-ketone (PEEK) were systematically studied. Additive manufacturing provides a novel and robust way to prepare medical product with anatomic matched geometry and tailored mechanical performance.
